Thermoforming Vs. Injection Molding: Which Is Better for Manufacturing Plastic Parts?
Thermoforming Vs. Injection Molding: Which Is Better for Manufacturing Plastic Parts?
Exploring the differences between the thermoforming and injection molding processes, how they work, and which might be the better fit for your project.
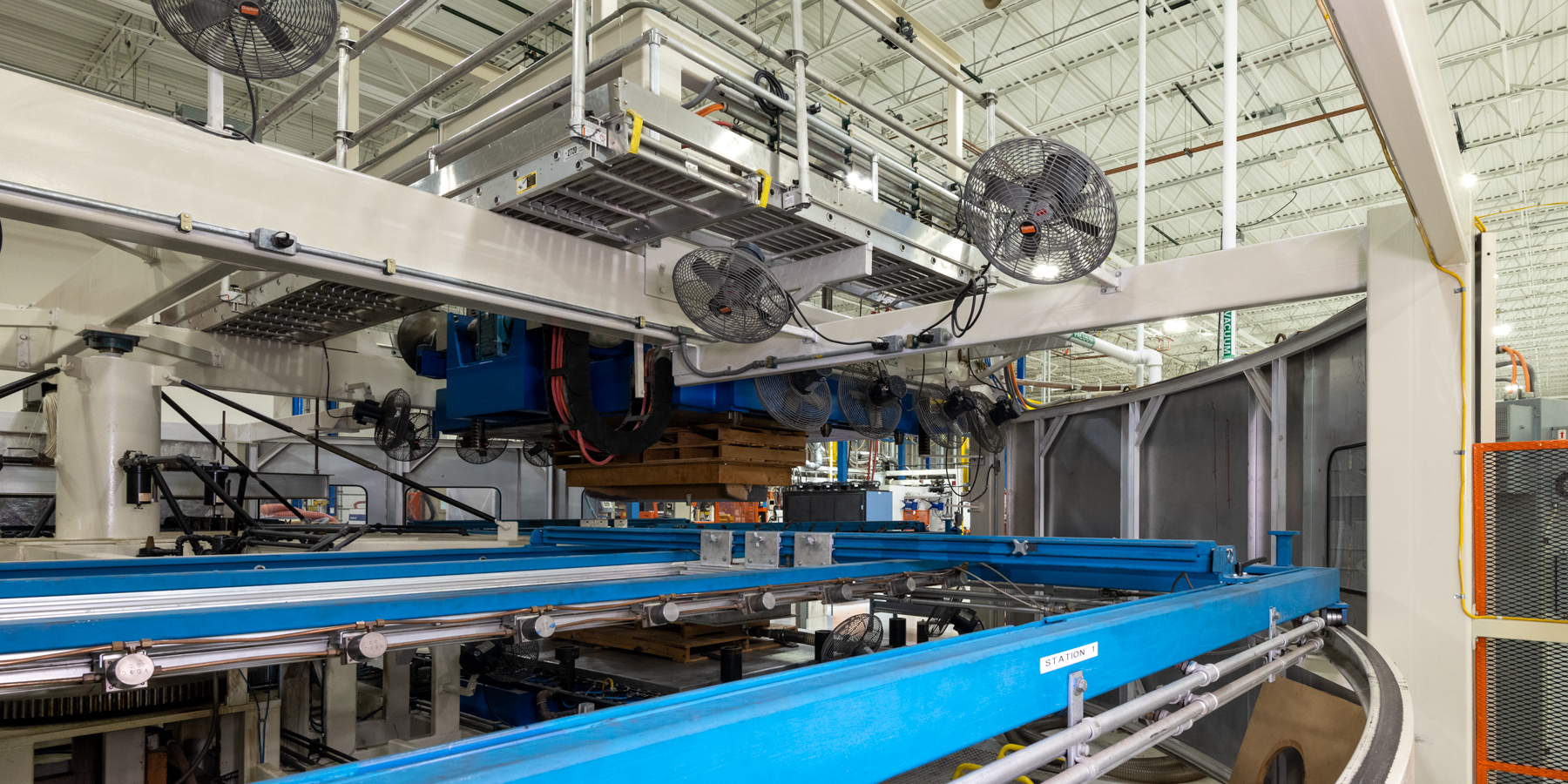
Two key methods are used in manufacturing plastic parts: thermoforming and injection molding. From transportation to packaging, these methods have applications in virtually every industry. Let’s explore how these processes work, the differences between them, and which might be the better fit for your project.
Understanding Thermoforming and Injection Molding
Thermoforming is the process of heating a plastic sheet until it's pliable, then forming it over a mold to create a finished part. This method is highly versatile, allowing manufacturers to produce both thick and thin-gauge plastic parts used in everything from airplane seat backs, automotive parts, bath surrounds, medical device housings, and signs to packaging.
Injection molding, on the other hand, involves melting plastic pellets and injecting them into a mold, where they cool and solidify into the desired shape. While injection molding is suitable for mass-producing small, intricate parts, it may not be the best fit for large or complex shapes.
Factor | Thermoforming | Injection Molding |
---|---|---|
Cost | More cost-effective for low to medium production volumes. | Higher initial costs due to expensive molds. |
Lead Time | Faster turnaround for prototypes and production. | Longer lead times due to more complex mold-making process. |
Part Size | Ideal for large, lightweight parts (e.g., airplane tray tables). | Typically used for smaller, more intricate parts. |
Material Flexibility | Can use a variety of plastic sheet materials (like Royalite®) for different applications. | Limited to materials that work well in the injection process. |
Customization | Easier to modify molds for quick changes or iterations. | Expensive to modify molds once created. |
Thermoforming Is Everywhere
You may not realize it, but thermoforming plays a significant role in everyday products—whether it's the seatback on an airplane or the yogurt container that held your breakfast this morning. Thermoforming's cost-effectiveness, speed, and versatility make it one of our go-to engineered solutions at Spartech. Here are just a few of the reasons we love it:
- Cost-Effective for Smaller Runs: Thermoforming’s lower tooling costs make it an affordable option for smaller production runs or custom parts. Unlike injection molding, which requires expensive steel or aluminum molds, thermoforming uses simpler tooling, significantly lowering upfront costs. Whether you're a large company or a startup, thermoforming offers flexibility without breaking the bank.
- Faster Turnaround Time: Parts can be produced and delivered more quickly with thermoforming than with other processes. Because the molds are simpler and easier to create, we can reduce lead times. This makes thermoforming an ideal solution for companies needing quick prototypes or a rapid response to market demand.
- Size and Shape Versatility: Thermoforming shines for creating large or complex parts for various applications. It’s commonly used for large items like interior and exterior parts for heavy trucks and agricultural equipment, spas, and airplane parts such as luggage doors, and armrests—components that would be costly or inefficient to produce using injection molding. Thermoforming can also handle deep and intricate shapes more efficiently, providing greater design freedom.
- Material Selection and Sustainability: Thermoforming offers a broader range of material choices, including environmentally friendly options like recycled or biodegradable plastics. This not only supports sustainability efforts but also allows manufacturers to tailor the material properties to the specific needs of the project—whether it’s durability, flexibility, or UV resistance.
- Scalability: Thermoforming is suitable for both low and high production volumes. Whether you're producing a few hundred units or scaling to thousands, thermoforming can meet your needs without the high costs associated with retooling or mold modifications in injection molding.
Applications of Thermoforming
Thanks to its adaptability, thermoforming is used across industries. Here are a few examples:
- Aerospace:Thermoformed parts are ideal for interior panels and structural components thatrequire lightweight yet durable materials that need to be flame rated.
- Healthcare & Medical:Medical trays and equipment enclosures are often thermoformed due to their need for precise, customizable designs.
- Transportation:Thermoformed parts are used in vehicles for interior and exterior parts such as floormats, truck cab walls, dashboard components, fender flares and tonneau covers, where complex shapes made from highly weatherable yet lightweight materials are essential.
- Packaging:Thermoforming is perfect for creating clamshells, blister packs, and custom trays that display products while also protecting them.
Check out the video below to see how we use thermoforming at Spartech to produce a variety of aerospace products:
If you're looking to develop high-quality, large, or complex plastic components, thermoforming may be the option for you.
Spartech would love to help bring your next thermoforming project to life. We specialize in producing high-quality thermoformed plastic parts, sheets, and rollstock for a variety of industries. Plus, our Innovation Center is continually developing new materials like Royalite® to meet the evolving demands of our customers. Whether you’re working on a new product design or looking to optimize your manufacturing process, we offer customized solutions for businesses of all sizes. Please reach out if you’re interested in learning more.
February 11, 2025